Лазерно заваряване
През последните години, благодарение на бързото развитие на новата енергийна индустрия, лазерното заваряване бързо навлезе в цялата нова енергийна индустрия поради своите бързи и стабилни предимства.Сред тях оборудването за лазерно заваряване представлява най-висок дял приложения в цялата нова енергийна индустрия.
Лазерното заваряване бързо се превърна в първия избор във всички сфери на живота поради бързата си скорост, голямата дълбочина и малката деформация.От точкови заварки до челни заварки, натрупване и запечатване, лазерното заваряване осигурява несравнима прецизност и контрол.Той играе важна роля в промишленото производство и производството, включително военната промишленост, медицинските грижи, космическата промишленост, 3C авточасти, механични ламаринени метали, нова енергия и други индустрии.
В сравнение с други технологии за заваряване, лазерното заваряване има своите уникални предимства и недостатъци.
Предимство:
1. Бърза скорост, голяма дълбочина и малка деформация.
2. Заваряването може да се извърши при нормална температура или при специални условия, а заваръчното оборудване е просто.Например, лазерен лъч не се движи в електромагнитно поле.Лазерите могат да заваряват във вакуум, въздух или определени газови среди и могат да заваряват материали, които са през стъкло или прозрачни за лазерния лъч.
3. Може да заварява огнеупорни материали като титан и кварц, както и да заварява различни материали с добри резултати.
4. След като лазерът е фокусиран, плътността на мощността е висока.Съотношението на страните може да достигне 5:1 и може да достигне до 10:1 при заваряване на устройства с висока мощност.
5. Може да се извърши микро заваряване.След като лазерният лъч се фокусира, може да се получи малко петно, което може да се позиционира точно.Може да се прилага за сглобяване и заваряване на микро и малки детайли за постигане на автоматизирано масово производство.
6. Може да заварява труднодостъпни места и да извършва безконтактно заваряване на дълги разстояния с голяма гъвкавост.Особено през последните години технологията за лазерна обработка на YAG възприе технология за предаване на оптични влакна, което позволи по-широко популяризиране и прилагане на технологията за лазерно заваряване.
7. Лазерният лъч е лесен за разделяне във времето и пространството и множество лъчи могат да се обработват на множество места едновременно, осигурявайки условия за по-прецизно заваряване.
Дефект:
1. Изисква се точността на сглобяване на детайла да бъде висока и позицията на гредата върху детайла не може да бъде значително отклонена.Това е така, защото размерът на лазерното петно след фокусиране е малък и заваръчният шев е тесен, което затруднява добавянето на добавъчни метални материали.Ако точността на сглобяване на детайла или точността на позициониране на гредата не отговарят на изискванията, има вероятност да възникнат дефекти при заваряване.
2. Цената на лазерите и свързаните с тях системи е висока, а еднократната инвестиция е голяма.
Често срещани дефекти при лазерно заваряване при производството на литиеви батерии
1. Порьозност при заваряване
Често срещани дефекти при лазерното заваряване са порите.Заваръчната разтопена вана е дълбока и тясна.По време на процеса на лазерно заваряване азотът нахлува в разтопения басейн отвън.По време на процеса на охлаждане и втвърдяване на метала, разтворимостта на азота намалява с намаляването на температурата.Когато разтопеният метал се охлади, за да започне да кристализира, разтворимостта ще спадне рязко и внезапно.По това време голямо количество газ ще се утаи и ще образува мехурчета.Ако скоростта на плаване на мехурчетата е по-малка от скоростта на кристализация на метала, ще се генерират пори.
В приложенията в производството на литиеви батерии често откриваме, че е особено вероятно да се появят пори по време на заваряването на положителния електрод, но рядко се появяват по време на заваряването на отрицателния електрод.Това е така, защото положителният електрод е направен от алуминий, а отрицателният електрод е направен от мед.По време на заваряване течният алуминий на повърхността е кондензирал преди вътрешният газ да прелее напълно, предотвратявайки преливането на газа и образуването на големи и малки дупки.Малки устицата.
В допълнение към причините за порите, споменати по-горе, порите също включват външен въздух, влага, повърхностно масло и т.н. Освен това посоката и ъгълът на издухване на азот също ще повлияят на образуването на пори.
Що се отнася до това как да се намали появата на заваръчни пори?
Първо, преди заваряване маслените петна и примесите по повърхността на входящите материали трябва да бъдат почистени навреме;в производството на литиеви батерии проверката на входящия материал е важен процес.
Второ, потокът на защитния газ трябва да се регулира според фактори като скорост на заваряване, мощност, позиция и т.н., и не трябва да бъде нито твърде голям, нито твърде малък.Налягането на защитната мантия трябва да се регулира според фактори като мощност на лазера и позиция на фокуса и не трябва да бъде нито твърде високо, нито твърде ниско.Формата на дюзата на защитното наметало трябва да се регулира според формата, посоката и други фактори на заваръчния шев, така че защитното наметало да може равномерно да покрие зоната на заваряване.
Трето, контролирайте температурата, влажността и праха във въздуха в цеха.Температурата и влажността на околната среда ще повлияят на съдържанието на влага на повърхността на субстрата и на защитния газ, което от своя страна ще повлияе на генерирането и изтичането на водни пари в разтопения басейн.Ако температурата и влажността на околната среда са твърде високи, ще има твърде много влага на повърхността на основата и защитния газ, генерирайки голямо количество водна пара, което води до пори.Ако температурата и влажността на околната среда са твърде ниски, ще има твърде малко влага на повърхността на субстрата и в защитния газ, намалявайки генерирането на водна пара, като по този начин намалява порите;нека персоналът по качеството открие целевата стойност на температурата, влажността и праха в заваръчната станция.
Четвърто, методът на люлеене на лъча се използва за намаляване или премахване на порите при лазерно заваряване с дълбоко проникване.Поради добавянето на люлеене по време на заваряване, възвратно-постъпателното люлеене на гредата към заваръчния шев причинява многократно претопяване на част от заваръчния шев, което удължава времето на престой на течния метал в заваръчната вана.В същото време отклонението на гредата също увеличава вложената топлина на единица площ.Съотношението дълбочина към ширина на заваръчния шев е намалено, което благоприятства появата на мехурчета, като по този начин се елиминират порите.От друга страна, люлеенето на лъча кара малкия отвор да се люлее съответно, което може също да осигури сила на разбъркване за заваръчния басейн, да увеличи конвекцията и разбъркването на заваръчния басейн и да има благоприятен ефект върху елиминирането на порите.
Пето, импулсната честота, импулсната честота се отнася до броя на импулсите, излъчвани от лазерния лъч за единица време, което ще повлияе на входящата топлина и натрупването на топлина в разтопения басейн и след това ще повлияе на температурното поле и полето на потока в разтопения басейн басейн.Ако честотата на импулса е твърде висока, това ще доведе до прекомерно внасяне на топлина в басейна с разтопена маса, причинявайки температурата на басейна с разтопена маса да бъде твърде висока, произвеждайки метални пари или други елементи, които са летливи при високи температури, което води до пори.Ако честотата на импулса е твърде ниска, това ще доведе до недостатъчно натрупване на топлина в разтопения басейн, което води до твърде ниска температура на разтопения басейн, намалявайки разтварянето и изтичането на газ, което води до пори.Най-общо казано, честотата на импулса трябва да бъде избрана в рамките на разумен диапазон въз основа на дебелината на субстрата и мощността на лазера и избягвайте да бъде твърде висока или твърде ниска.
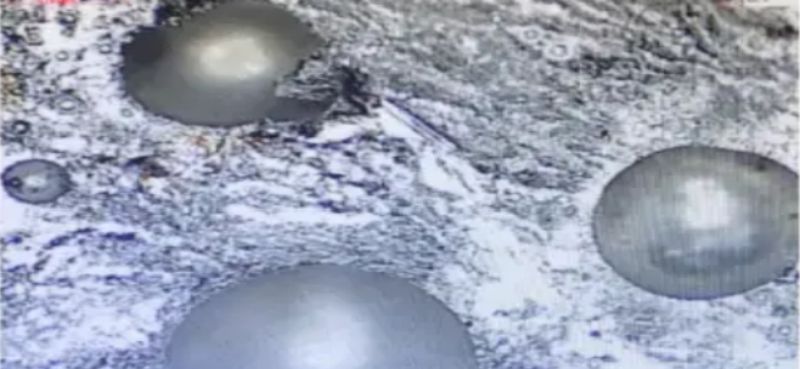
Отвори за заваряване (лазерно заваряване)
2. Заваръчни пръски
Пръските, генерирани по време на процеса на заваряване, лазерното заваряване ще повлияят сериозно на качеството на повърхността на заваръчния шев и ще замърсят и повредят лещата.Общата производителност е следната: след завършване на лазерното заваряване много метални частици се появяват на повърхността на материала или детайла и се придържат към повърхността на материала или детайла.Най-интуитивното представяне е, че при заваряване в режим на галванометър, след период на използване на защитната леща на галванометъра, на повърхността ще има плътни вдлъбнатини, които се причиняват от заваръчни пръски.След дълго време е лесно да блокирате светлината и ще има проблеми със заваръчната светлина, което води до поредица от проблеми като счупено заваряване и виртуално заваряване.
Какви са причините за пръскането?
Първо, плътността на мощността, колкото по-голяма е плътността на мощността, толкова по-лесно е да се генерират пръски, а пръските са пряко свързани с плътността на мощността.Това е вековен проблем.Поне досега индустрията не е успяла да реши проблема с пръскането и може само да каже, че той е леко намален.В индустрията за литиеви батерии пръскането е най-големият виновник за късо съединение на батерията, но то не е в състояние да разреши първопричината.Въздействието на пръските върху батерията може да бъде намалено само от гледна точка на защита.Например кръг от отвори за отстраняване на прах и защитни капаци са добавени около заваръчната част и редове от въздушни ножове са добавени в кръгове, за да се предотврати въздействието на пръски или дори повреда на батерията.Може да се каже, че унищожаването на околната среда, продуктите и компонентите около станцията за заваряване е изчерпало средствата.
Що се отнася до решаването на проблема с пръскането, може да се каже само, че намаляването на заваръчната енергия помага за намаляване на пръскането.Намаляването на скоростта на заваряване също може да помогне, ако проникването е недостатъчно.Но при някои специални изисквания на процеса, това има малък ефект.Това е един и същ процес, различни машини и различни партиди материали имат напълно различни ефекти на заваряване.Следователно в новата енергийна индустрия има неписано правило, един набор от параметри на заваряване за едно оборудване.
Второ, ако повърхността на обработвания материал или детайла не е почистена, маслените петна или замърсителите също ще причинят сериозни пръски.По това време най-лесно е да почистите повърхността на обработвания материал.
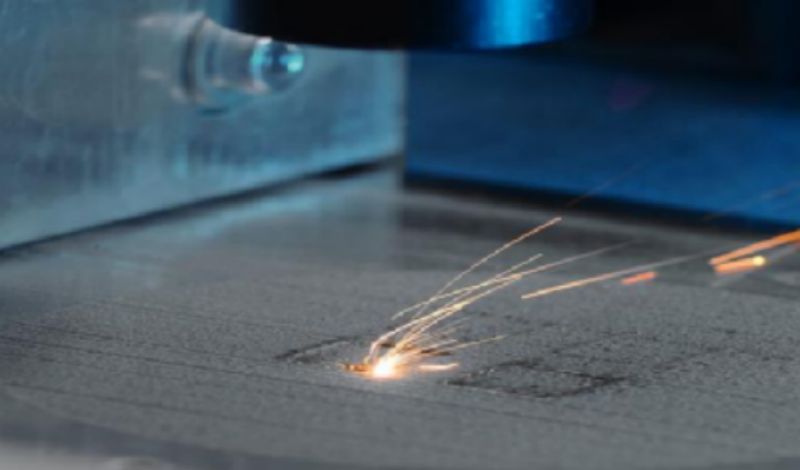
3. Висока отразяваща способност на лазерното заваряване
Най-общо казано, високото отражение се отнася до факта, че материалът за обработка има малко съпротивление, относително гладка повърхност и ниска степен на абсорбция за лазери в близката инфрачервена област, което води до голямо количество лазерно излъчване и тъй като повечето лазери се използват вертикално Поради материала или малък наклон, връщащата се лазерна светлина навлиза отново в изходната глава и дори част от връщащата се светлина се свързва в предаващото енергия влакно и се предава обратно по влакното навътре на лазера, което прави основните компоненти вътре в лазера да продължат да бъдат при висока температура.
Когато отразяващата способност е твърде висока по време на лазерно заваряване, могат да се вземат следните решения:
3.1 Използвайте антирефлексно покритие или третирайте повърхността на материала: покриването на повърхността на заваръчния материал с антирефлексно покритие може ефективно да намали отразяващата способност на лазера.Това покритие обикновено е специален оптичен материал с ниска отразяваща способност, който абсорбира лазерната енергия, вместо да я отразява обратно.При някои процеси, като заваряване на токоприемник, мека връзка и др., повърхността може да бъде и релефна.
3.2 Регулиране на ъгъла на заваряване: Чрез регулиране на ъгъла на заваряване лазерният лъч може да пада върху заваръчния материал под по-подходящ ъгъл и да намали появата на отражение.Обикновено падането на лазерния лъч перпендикулярно на повърхността на материала, който ще се заварява, е добър начин за намаляване на отраженията.
3.3 Добавяне на допълнителен абсорбент: По време на процеса на заваряване към заваръчния шев се добавя определено количество допълнителен абсорбент, като прах или течност.Тези абсорбери абсорбират лазерната енергия и намаляват отразяващата способност.Подходящият абсорбент трябва да бъде избран въз основа на специфичните заваръчни материали и сценарии на приложение.В индустрията на литиевите батерии това е малко вероятно.
3.4 Използвайте оптични влакна за предаване на лазер: Ако е възможно, оптични влакна могат да се използват за предаване на лазер към позицията на заваряване, за да се намали отразяващата способност.Оптичните влакна могат да насочват лазерния лъч към зоната на заваряване, за да се избегне директно излагане на повърхността на заваръчния материал и да се намали появата на отражения.
3.5 Регулиране на параметрите на лазера: Чрез регулиране на параметри като лазерна мощност, фокусно разстояние и фокусен диаметър, разпределението на лазерната енергия може да се контролира и отраженията могат да бъдат намалени.За някои отразяващи материали намаляването на лазерната мощност може да бъде ефективен начин за намаляване на отраженията.
3.6 Използвайте разделител на лъчи: Разделителят на лъчи може да насочи част от лазерната енергия към абсорбционното устройство, като по този начин намалява появата на отражения.Устройствата за разделяне на лъча обикновено се състоят от оптични компоненти и абсорбери и чрез избор на подходящи компоненти и регулиране на оформлението на устройството може да се постигне по-ниска отразяваща способност.
4. Заваръчен подрез
В процеса на производство на литиева батерия кои процеси е по-вероятно да причинят подбиване?Защо се получава подбиване?Нека го анализираме.
Подрязване, като цяло суровините за заваряване не са добре комбинирани помежду си, празнината е твърде голяма или се появява жлебът, дълбочината и ширината са основно по-големи от 0,5 mm, общата дължина е по-голяма от 10% от дължината на заварката или по-голяма от стандарта на продуктовия процес на исканата дължина.
В целия процес на производство на литиева батерия е по-вероятно да възникне подбиване и то обикновено се разпределя в предварителното заваряване и заваряването на цилиндричната покривна плоча и предварителното заваряване и заваряването на квадратната алуминиева обвивка.Основната причина е, че уплътнителната покривна плоча трябва да си сътрудничи с обвивката при заваряване, процесът на съвпадение между уплътнителната покривна плоча и обвивката е предразположен към прекомерни заваръчни празнини, жлебове, колапс и т.н., така че е особено предразположен към подрязвания .
И така, какво причинява подбиването?
Ако скоростта на заваряване е твърде висока, течният метал зад малкия отвор, сочещ към центъра на заваръчния шев, няма да има време да се преразпредели, което води до втвърдяване и подрязване от двете страни на заваръчния шев.С оглед на горната ситуация трябва да оптимизираме параметрите на заваряване.Казано по-просто, това са повтарящи се експерименти за проверка на различни параметри и продължаване на DOE, докато се намерят подходящите параметри.
2. Прекомерните междини на заваръчните шевове, бразди, срутвания и т.н. на заваръчните материали ще намалят количеството разтопен метал, запълващ празнините, което ще направи по-вероятно да се появят подрязвания.Това е въпрос на оборудване и суровини.Дали суровините за заваряване отговарят на изискванията за входящи материали на нашия процес, дали точността на оборудването отговаря на изискванията и т.н. Нормалната практика е постоянно да измъчваме и бием доставчиците и хората, които отговарят за оборудването.
3. Ако енергията спадне твърде бързо в края на лазерното заваряване, малката дупка може да се срути, което да доведе до локално подрязване.Правилното съвпадение на мощност и скорост може ефективно да предотврати образуването на подрязвания.Както се казва в старата поговорка, повторете експериментите, проверете различни параметри и продължете DOE, докато намерите правилните параметри.
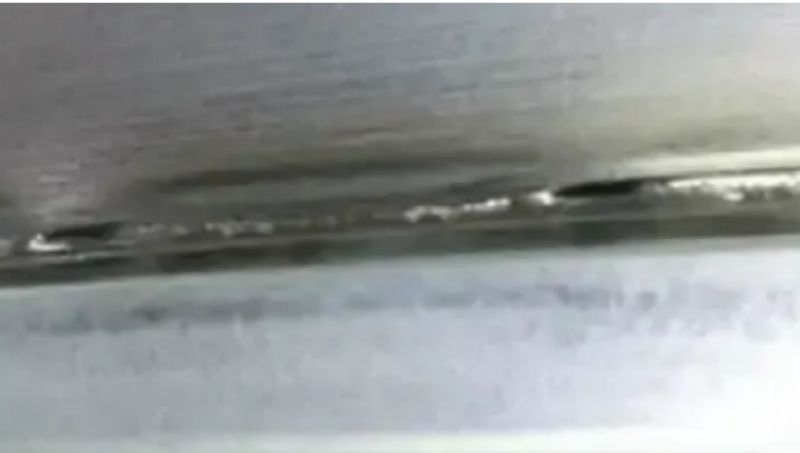
5. Колапс на центъра на заваръчния шев
Ако скоростта на заваряване е ниска, разтопеният басейн ще бъде по-голям и по-широк, увеличавайки количеството разтопен метал.Това може да затрудни поддържането на повърхностното напрежение.Когато разтопеният метал стане твърде тежък, центърът на заваръчния шев може да потъне и да образува вдлъбнатини и вдлъбнатини.В този случай енергийната плътност трябва да бъде подходящо намалена, за да се предотврати срутването на стопилката.
В друга ситуация, заваръчната междина просто образува колапс, без да причинява перфорация.Това несъмнено е проблем с прилягането на оборудването.
Правилното разбиране на дефектите, които могат да възникнат по време на лазерно заваряване и причините за различни дефекти, позволява по-целенасочен подход за разрешаване на необичайни проблеми със заваряването.
6. Заварени пукнатини
Пукнатините, които се появяват по време на непрекъснато лазерно заваряване, са главно термични пукнатини, като кристални пукнатини и пукнатини от втечняване.Основната причина за тези пукнатини са големите сили на свиване, генерирани от заваръчния шев, преди да се втвърди напълно.
Има и следните причини за пукнатини при лазерно заваряване:
1. Неразумно проектиране на заваръчния шев: Неправилният дизайн на геометрията и размера на заваръчния шев може да причини концентрация на напрежението при заваряване, като по този начин причини пукнатини.Решението е да се оптимизира конструкцията на заваръчния шев, за да се избегне концентрацията на напрежението при заваряване.Можете да използвате подходящи офсетни заварки, да промените формата на заварката и т.н.
2. Несъответствие на заваръчните параметри: Неправилният избор на заваръчните параметри, като твърде висока скорост на заваряване, твърде висока мощност и т.н., може да доведе до неравномерни температурни промени в зоната на заваряване, което води до голямо напрежение при заваряване и пукнатини.Решението е да се настроят параметрите на заваряване, за да съответстват на конкретния материал и условията на заваряване.
3. Лоша подготовка на заваръчната повърхност: Неправилното почистване и предварителна обработка на заваръчната повърхност преди заваряване, като отстраняване на оксиди, мазнини и т.н., ще повлияе на качеството и здравината на заваръчния шев и лесно ще доведе до пукнатини.Решението е адекватно почистване и предварително третиране на заваръчната повърхност, за да се гарантира, че примесите и замърсителите в зоната на заваряване се третират ефективно.
4. Неправилен контрол на входящата топлина при заваряване: Лошият контрол на входящата топлина по време на заваряване, като прекомерна температура по време на заваряване, неправилна скорост на охлаждане на заваръчния слой и т.н., ще доведе до промени в структурата на зоната на заваряване, което води до пукнатини .Решението е да се контролира температурата и скоростта на охлаждане по време на заваряване, за да се избегне прегряване и бързо охлаждане.
5. Недостатъчно облекчаване на напрежението: Недостатъчното облекчаване на напрежението след заваряване ще доведе до недостатъчно облекчаване на напрежението в заварената зона, което лесно ще доведе до пукнатини.Решението е да се извърши подходяща обработка за облекчаване на напрежението след заваряване, като термична обработка или обработка с вибрации (основна причина).
Що се отнася до процеса на производство на литиеви батерии, кои процеси е по-вероятно да причинят пукнатини?
Обикновено пукнатините са склонни да се появят по време на заваряване на запечатване, като заваряване на цилиндрични стоманени или алуминиеви черупки, заваряване на квадратни алуминиеви черупки и т.н. до пукнатини.
Разбира се, можем също да използваме тел за пълнене, предварително нагряване или други методи за намаляване или премахване на тези пукнатини.
Време на публикуване: 01 септември 2023 г